الحار منتجات
ملكنا الإخبارية
pm of a ball mill
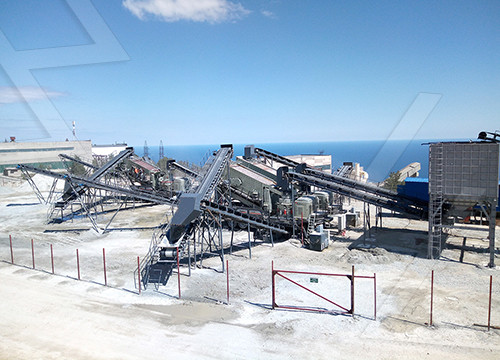
行星式球磨仪 PM 100 RETSCH
Download. The Planetary Ball Mill PM 100 is a powerful benchtop model with a single grinding station and an easy-to-use counterweight which compensates masses up to 8 kg. It allows for grinding up to 220 ml sample material per batch. The extremely high
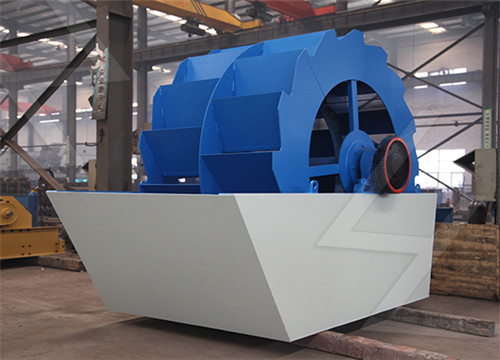
行星式球磨仪PM100CM-德国RETSCH(莱驰)研磨仪
行星式球磨仪 PM 100 CM. The Planetary Ball Mill PM 100 CM is a powerful benchtop model with a single grinding station and an easy-to-use counterweight which compensates masses up to 8 kg. It allows for
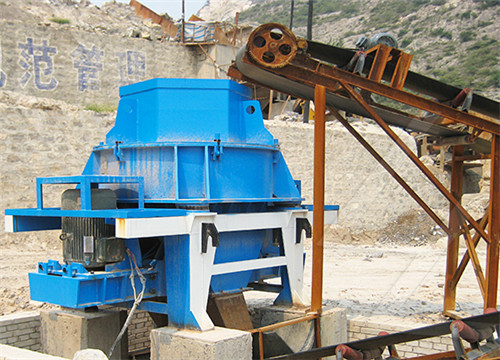
Planetary Ball Mill PM 100 RETSCH highest
The Planetary Ball Mill PM 100 is a powerful benchtop model with a single grinding station and an easy-to-use counterweight which compensates
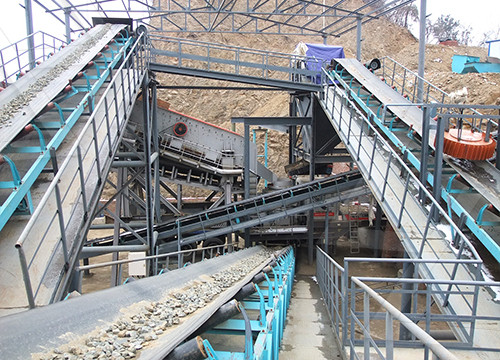
Ball Mill an overview ScienceDirect Topics
where d b.max is the maximum size of feed (mm); σ is compression strength (MPa); E is modulus of elasticity (MPa); ρb is density of material of balls (kg/m 3); D is inner diameter
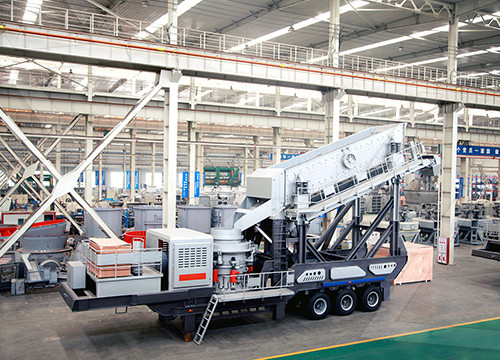
Ball Mill Design/Power Calculation Mineral
2015年6月19日 Ball Mill Power Calculation Example #1. A wet grinding ball mill in closed circuit is to be fed 100 TPH of a material with a work index
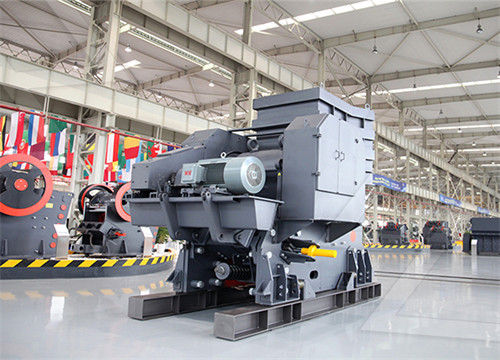
Best way to determine the ball-to-powder ratio in ball
2015年4月2日 The maximum power draw in ball mill is when ball bed is 35-40 % by volume in whole empty mill volume. Considering that ball bed has a porosity of 40 %, the actual
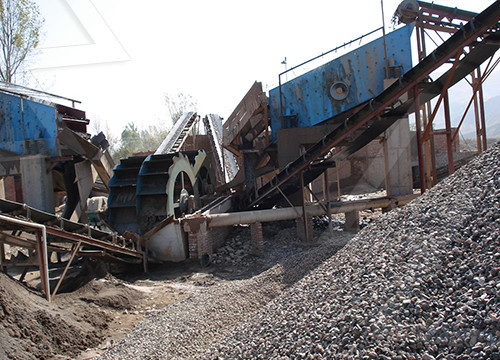
Ball Mill Parameter SelectionCalculation JXSC
2019年8月30日 1 Calculation of ball mill capacity. The production capacity of the ball mill is determined by the amount of material required to be ground, and it must have a certain
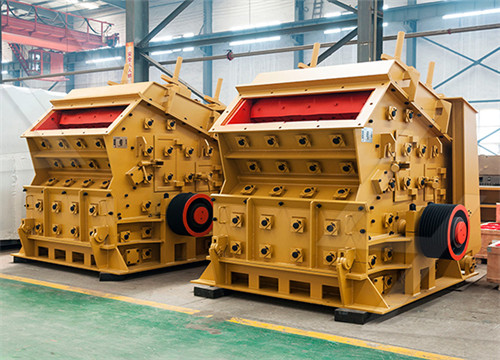
How Many Balls in a Ball Mill? JXSC Machine
2019年12月19日 During the running-in process, the amount of steel balls is added for the first time, which accounts for 80% of the maximum ball load of the ball mill. Steel ball
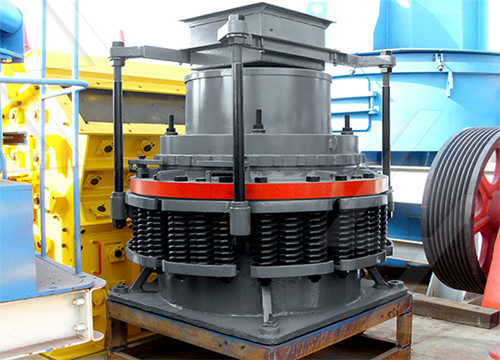
Grinding time for ball mills GrindingClassification
2023年4月6日 For ball milling, you can assume a porosity of about 0.35 to 0.40 (the volume of space between the balls) and you can normally assume the pulp surface level
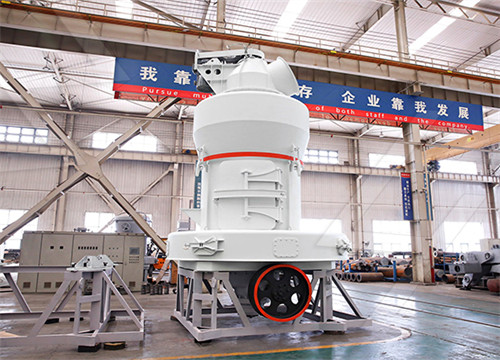
en/pm of a ball mill.md at main dinglei2022/en
Contribute to dinglei2022/en development by creating an account on GitHub.
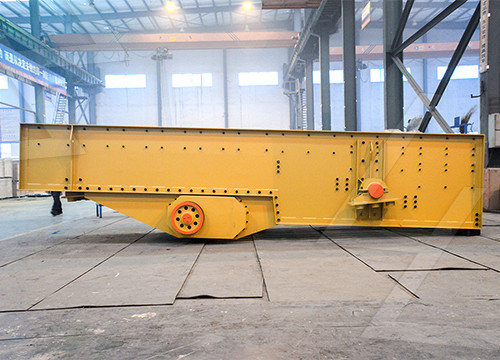
Planetary Ball Mill PM 100 RETSCH highest
The Planetary Ball Mill PM 100 is a powerful benchtop model with a single grinding station and an easy-to-use counterweight which compensates masses up to 8 kg. It allows for grinding up to 220 ml sample material
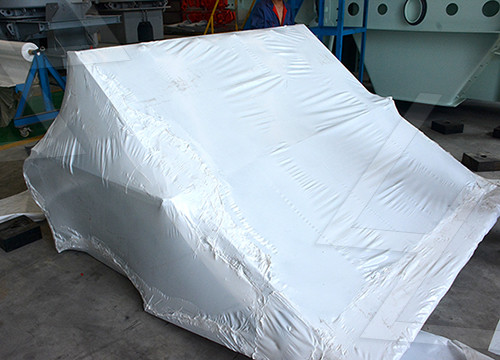
(PDF) Process Engineering with Planetary Ball
2013年2月7日 [220][221][222][223][224] As it is known, planetary ball mills are the most common and effective equipment that used for a homogeneous powder mixing process. 221,225, 226 A homogeneous powder
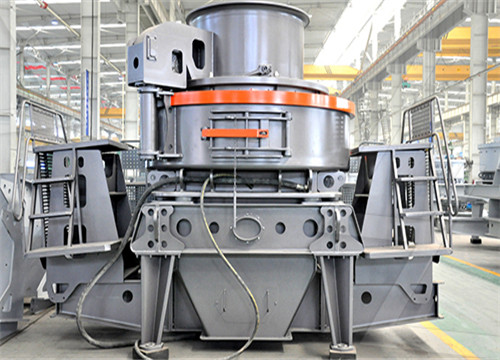
Ammonia synthesis by mechanocatalysis in a ball mill
2021年10月25日 The result is a thin but continuous stream of ammonia. Unimagined effect: The grinding process in a ball mill activates a catalyst in such a way that it facilitates the synthesis of ammonia at a much lower temperature and pressure than is necessary in the well-established Haber-Bosch process. Five hundred degrees Celsius and 200 bar
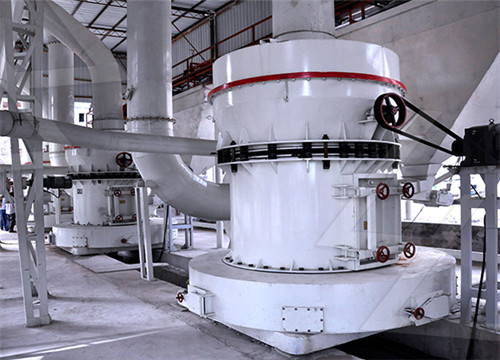
(PDF) Grinding in Ball Mills: Modeling and
2012年6月1日 The vibratory ball mill (VBM, Sweco, Belgium) consists of a 36 L-capacity grinding chamber made of an abrasion-resistant elastomer, put in vibrating motion by high-tensile steel springs [28].
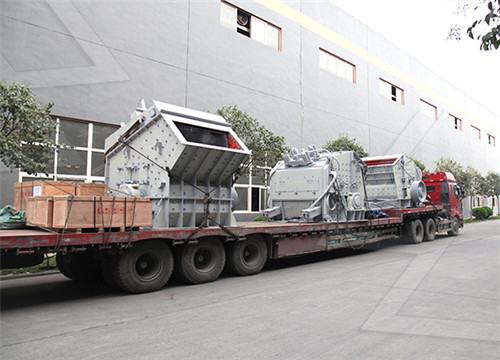
Ball Mill Working Principle And Main Parts GitHub Pages
2015年7月14日 Ball Mill Working Principle. To be chosen according to the grinding material, material is composed of a ball mill feed end of the hollow shaft is arranged in the tube body, when the ball mill cylinder rotation time, grinding body due to inertia and centrifugal force, the effects of friction, making it attached to the cylinder liner on the
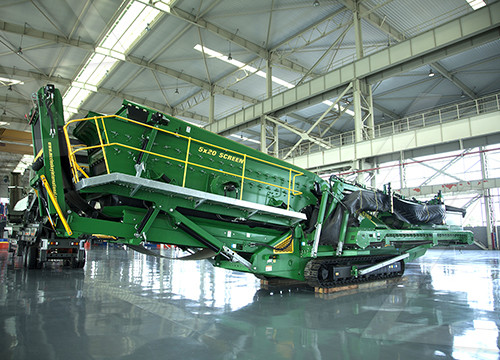
How to Make a Ball Mill: 12 Steps (with Pictures)
2020年8月10日 Position the pieces so that the base sits at a height of 4” (10.16 cm). You can secure the pieces in place with some
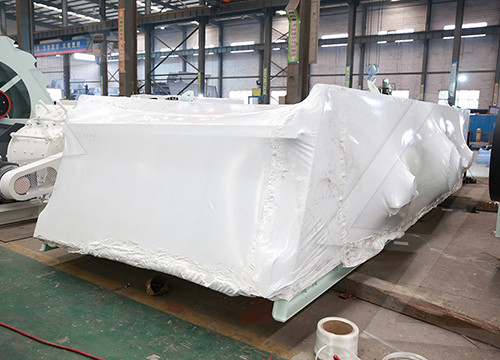
Grinding time for ball mills GrindingClassification
2023年4月6日 For ball milling, you can assume a porosity of about 0.35 to 0.40 (the volume of space between the balls) and you can normally assume the pulp surface level is equal to the ball charge surface level. So do a crash-stop and measure the volumetric filling of the charge, then multiply that volume by 0.35 or 0.40.
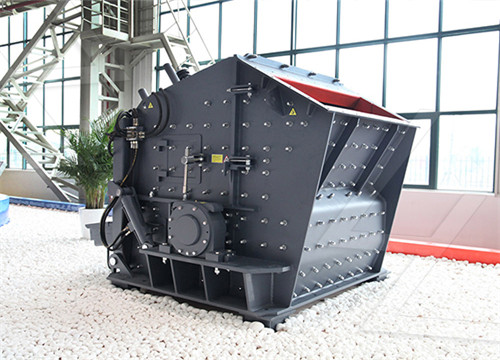
Finite Element and Multibody Dynamics Analysis of a Ball
For this purpose, a glass crusher machine based on the ball mill concept is designed to transform glass waste into powder of 2 mm particle size. The main enhanced features of this machine with respect to state-of-the-art designs are the continuous feed aspect and the powder discharge technique. The design methodology consisted of mathematical
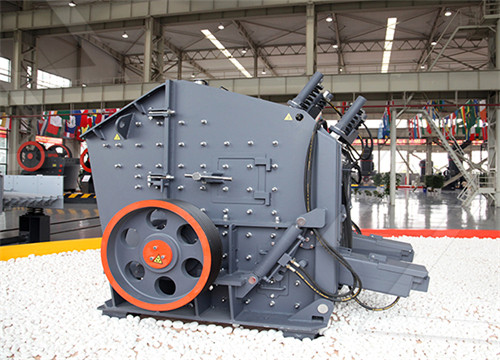
Construction and Working of Ball Mill Solution Parmacy
2021年5月11日 Construction of Ball Mill. The ball mill consists of a hollow metal cylinder mounted on a shaft and rotating about its horizontal axis. The cylinder can be made of metal, porcelain, or rubber. Inside the cylinder balls or pebbles are placed. The balls occupy between 30 and 50% of the volume of the cylinder. The diameter of the balls depends on
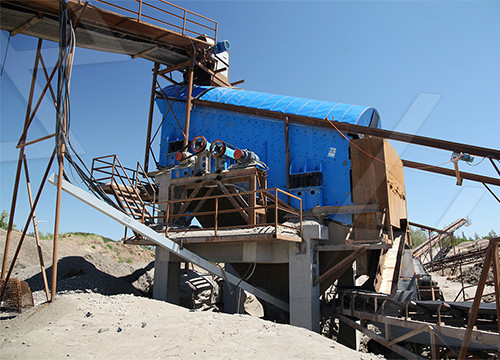
How Many Balls in a Ball Mill? JXSC Machine
2019年12月19日 During the running-in process, the amount of steel balls is added for the first time, which accounts for 80% of the maximum ball load of the ball mill. Steel ball sizes are Φ120㎜, Φ100㎜, Φ80㎜, Φ60㎜, Φ40㎜. For example, the 100-150 tons ball mill has a maximum ball loading capacity of 9.5-10 tons. For the first time, 30% 40% of
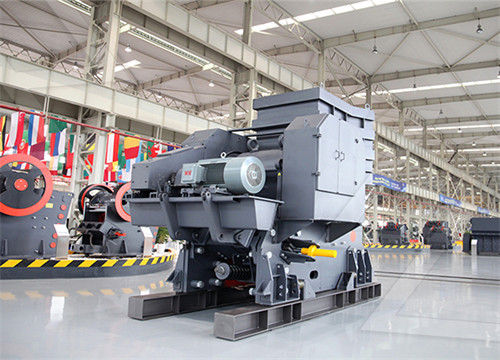
Ball milling: a green technology for the preparation and
The ball mill Ball milling is a mechanical technique widely used to grind powders into ne particles and blend materials.18 Being an environmentally-friendly, cost-effective technique, it has found wide application in industry all over the world. Since this mini-review mainly focuses on the conditions applied for the prep-
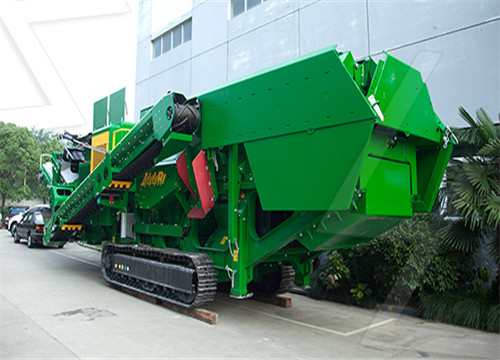
Industrial Ball Mills: Steel Ball Mills and Lined Ball Mills
2 之 Steel Ball MillsLined Ball Mills. Particle size reduction of materials in a ball mill with the presence of metallic balls or other media dates back to the late 1800’s. The basic construction of a ball mill is a cylindrical container with journals at its axis. The cylinder is filled with grinding media (ceramic or metallic balls or rods
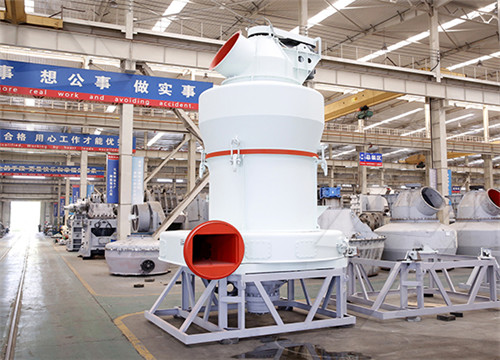
Ball Mill Parameter SelectionCalculation JXSC
2019年8月30日 1 Calculation of ball mill capacity. The production capacity of the ball mill is determined by the amount of material required to be ground, and it must have a certain margin when designing and selecting. There are many factors affecting the production capacity of the ball mill, in addition to the nature of the material (grain size, hardness,
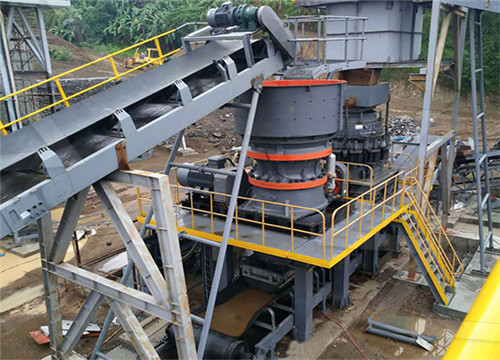
Ball Mills Glen Mills, Inc.
2022年4月17日 The E max is an entirely new type of ball mill for high energy milling. The unique combination of high friction and impact results in extremely fine particles within the shortest amount of time. SKU: n/a. Add to Wishlist. Compare. GrindingMilling, Planetary Ball Mills PM 100 Planetary Ball Mill. GrindingMilling, Planetary Ball Mills PM
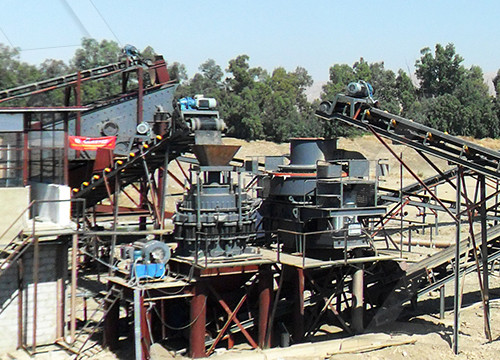
Laboratory Mills MRC-Lab
A typical type of fine grinder is the ball mill. A slightly inclined or horizontal rotating cylinder is partially filled with balls, usually stone or metal, which grinds material to the necessary fineness by friction and impact with the tumbling balls. Ball mills normally operate with an approximate ball charge of 30%.
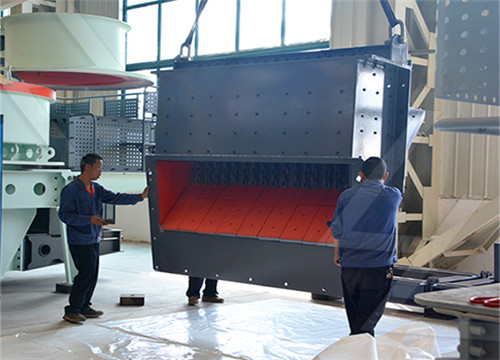
Finite Element and Multibody Dynamics Analysis of a Ball
For this purpose, a glass crusher machine based on the ball mill concept is designed to transform glass waste into powder of 2 mm particle size. The main enhanced features of this machine with respect to state-of-the-art designs are the continuous feed aspect and the powder discharge technique. The design methodology consisted of mathematical
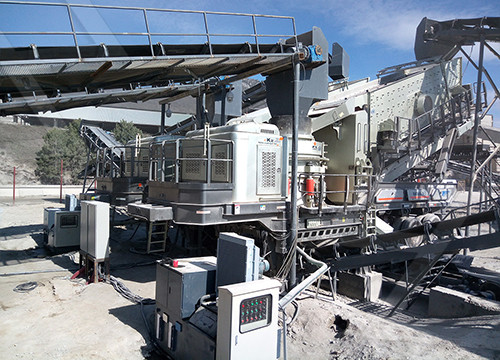
How Many Balls in a Ball Mill? JXSC Machine
2019年12月19日 During the running-in process, the amount of steel balls is added for the first time, which accounts for 80% of the maximum ball load of the ball mill. Steel ball sizes are Φ120㎜, Φ100㎜, Φ80㎜, Φ60㎜, Φ40㎜. For example, the 100-150 tons ball mill has a maximum ball loading capacity of 9.5-10 tons. For the first time, 30% 40% of
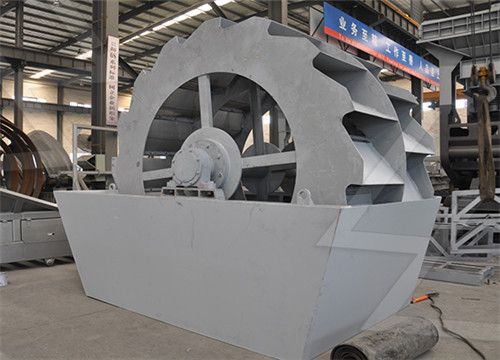
Grinding time for ball mills GrindingClassification
2023年4月6日 For ball milling, you can assume a porosity of about 0.35 to 0.40 (the volume of space between the balls) and you can normally assume the pulp surface level is equal to the ball charge surface level. So do a crash-stop and measure the volumetric filling of the charge, then multiply that volume by 0.35 or 0.40.
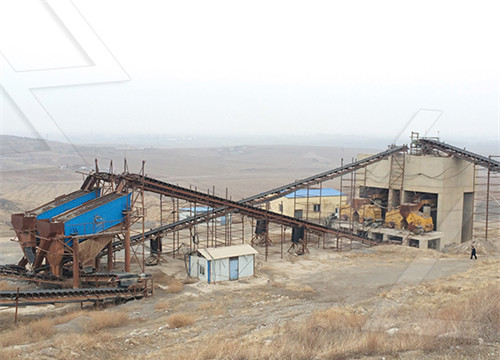
What it is the optimun speed for a ball mill ? Pyrotechnics
2006年10月19日 Posted 21 October 2006 04:24 PM. Congratulations on your ball mill! You'll want to further reduce your motor speed by 3:1 to mill more efficiently. Right now, your RPM is just slightly under the speed where the media won't do any work. The optimum speed for your jar to turn is around 90 RPM like Frozentech said.

Addition of DLC4LATB to the Series of Taper Ball Nose End
2022年2月9日 This is a product information page introducing Materials' new and existing products. [Addition of DLC4LATB to the Series of Taper Ball Nose End Mills for Machining Aluminium Alloy Impellers] information. Please find the most suitable product.
تستخدم على نطاق واسع منخفضة التكلفة كسارة الركام
مطاحن في الولايات المتحدة الأمريكية
مطحنة الرمل لمعالجة الفرن
مضخات المياه ستة بوصة للبيع
مطحنة الكرة بيركول نوع Bg U
شراء معدات ثقيلة بالتقسيط
اوج توخالی ساخت دستگاه بلوک
المطرقة مطحنة مع محرك
تهتز النطاط لمعالجة المعادن
اخبار ماكنة التصوير canon ir
قطع غيار طاحونة فائقة الرطب مادوراي
خام الذهب سحق تدفق معالجة الرسم البياني
آلات تكسير الرمل والحصى Songzi
المسار شنت كسارة الفك في مصر
آلة كسارة في عمان للبيع
هي طاحونة اليد
سعر مصنع كسارة الحجر 100 Tph
بررسی سنگ زنی الماس
كسارة تصادمية pb 200 250
طن الهند سعر الكرة مطحنة
حامض ساخن المعدات
تستخدم الطرق السريعة للسكك الحديدية كسارة الصدم pf
آلة طحن الحفر الأساسية sm
أوبيرغ مصفاة النفط محطم
غربال كسارة الحصى
أجزاء على شبكة الاتصالات العالمية من آلة الطحن كوم
حول لدينا
تأسست شركة Henan Lrate للعلوم والتكنولوجيا المحدودة التي تصنع معدات التكسير والطحن الكبيرة والمتوسطة الحجم في عام 1987. وهي شركة مساهمة حديثة مع البحث والتصنيع والمبيعات معًا.
على مدار أكثر من 30 عامًا ، تلتزم شركتنا بنظام الإدارة العلمية الحديث والتصنيع الدقيق والريادة والابتكار. الآن أصبحت LIMING رائدة في صناعة تصنيع الآلات المحلية والخارجية.